Achieving continuous improvement of operational efficiency and customer experience with RPA
Case Study: Improving customer experience through operational efficiencies
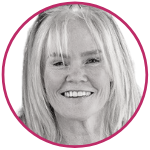
Dr. Jenny Dahlstrom
Acting Transformation Manager – Change/Lean,
Knox City Council (VIC)
The Journey Towards
Business Transformation
All large organisations, and public sector institutions in particular, generally have complicated, bureaucratic processes, developed over time. Some of these require a lot of repetitive employee input, whilst others were simply developed in a different age – before the digital age – and would benefit from an upgrade. These upgrades can take many forms, from Robotic Process Automation (RPA), to just a simple improvement or advancement in processes.
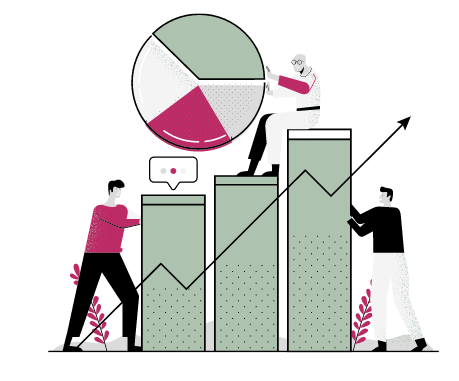
Jenny Dahlstrom, the Acting Transformation Manager – Change/Lean at Knox City Council in Melbourne’s east, says that knowing they needed to upgrade, they went “from Lean practice and thinking, to business transformation and business improvement.” It was a journey that took some time.
Like many councils, Knox is a fairly large institution. They cater for “164,500 residents, 30% of whom actually work in the city of Knox,” which is quite a high percentage compared to other councils. The average age of the residents “is around 39,” with an even gender split. To do all that the Council does, it has “about 1,100 employees.” The staff are ultimately there “to serve the community,” and in many ways, that means making regular decisions for the benefit of the community. Knox has a series of priority areas that all staff sign up to, and goal eight “is about having confidence in our decision-making.” In 2018, to better facilitate that process and live up to that goal, the Council introduced the concept of ‘Lean’, a project management toolset that emerged from the manufacturing industry and was implemented at Knox “to ensure that we had the most efficient and effective customer experience possible, and that we were delivering the best possible public value.”
In many ways, Lean is a “philosophy, a way of thinking and problem solving, a process of visual display and quick identification of problems through process mapping and the introduction of some key tools.” Lean has many benefits and served Knox well for two years. However, in June 2020, the Council decided that the next iteration might be called for, but began by doing “an extensive review.” This showed the Council executive that some things worked well, but there were also “opportunities to make some changes.” Largely this was because Lean “was born out of the automotive industry and thus some of the principles don’t work quite as well in a community service environment.” Quick identification of problems and solutions and plugging gaps is a good thing, but in a council, sometimes taking a little longer to come to a decision is better and more beneficial to the customer. Lean is mostly about quick fixes. It has its benefits, and thus the decision was made to broaden the focus “and move into the area of business improvement.”
Towards Business Improvement – A Cultural Evolution
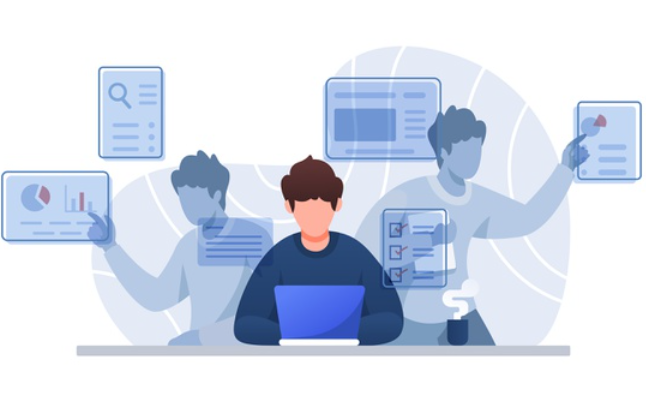
At Knox, “business improvement was really about making sure that we are able to justify our decision-making and make sure it is in the best interests of the community.” In many ways, it was “really about a cultural evolution” because many subtle things had to change. For instance, “we had to broaden some bits of work, redesign others and add some new perspectives.” One of the things that the review found was that “many of our projects were being driven from a project management perspective, not a people management perspective.” Since people and the community are supposed to be at the centre of all operations, this was not ideal. “So we introduced the notion of change management, which underpins the four other areas of business improvement activities:”
- Business strategy – The goal is “to become a trusted advisor to support business improvement at Knox.” This means “that we identify key business goals and priorities linked to the business strategy.” This came about “because we used to prioritise everything, so nothing was a priority.”
- Digitisation and automation – “This is about how we digitise, automate and enhance many of our processes. This ensures that change management is aligned to all of our ICT projects. For instance, moving from manual to automated human resources processing.”
- Analytics – “Problem and solution identification based on data. A Lean principle is that if you can’t measure or understand something, you can’t improve it. So this is about using analytics to measure and understand where we are at in order to go on a continuous improvement journey. Previously we didn’t understand our base levels so the journey was fundamentally flawed. Now we use data for better analysis and decision-making.”
- Business optimisation – “To improve, we review, evaluate and optimise our operations. This is where Lean kicks in, particularly through the introduction of ‘promap’ tools so we can understand where there’s double handling, or where there are opportunities to increase efficiencies.”
Part of the cultural evolution is to recognise these areas and embed them into practice, so that, for example, “if I see some double handling processes, it is actually offensive to my sensibilities.” The other part of it is to recognise that “structure should follow strategy, not the other way around.”
The full structural re-alignment is due to come into effect mid-year, but “we are also transitioning to a new CEO,” so that timeframe could be somewhat delayed. Either way, to support the change, a new “business improvement area” has been created, which also includes a “culture and strategy focus because we know that we need to link this to our structure and to our strategy.” The three areas of “strategy & business intelligence, transformation, and culture” all now “sit under one area,” which makes the whole process more seamless. Moving towards business improvement has also “freed up significant time and effort in the recruitment space,” since staff has more time and opportunity to work towards best practice.
Ideally, all of this is being done “to ensure that we are getting the best bang for our bucks as an organisation.” Now that the process has been completed and the re-alignment is almost a reality, it is clear that the process has contributed towards “better decision-making and is linked to our strategy, linked to day-to-day business improvement, linked directly to our ICT program, and linked to the process of digitisation and transformation.” All in all, this makes for better council processes, especially for the customer.
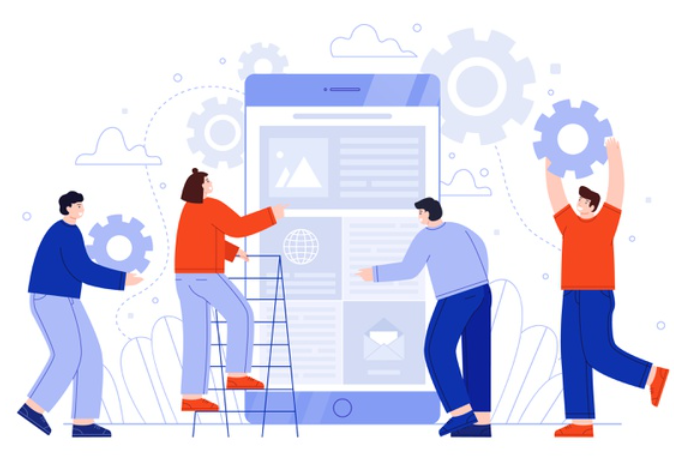